N.B. Het kan zijn dat elementen ontbreken aan deze printversie.
Nederlandse zonnepanelenfabriek Start-up Solarge opent deze maandag in Weert officieel een fabriek die made in the Netherlands-zonnepanelen levert, die beter zijn voor het milieu. Maar ook duurder. Of klanten dat ervoor willen betalen, moet de komende maanden gaan blijken.
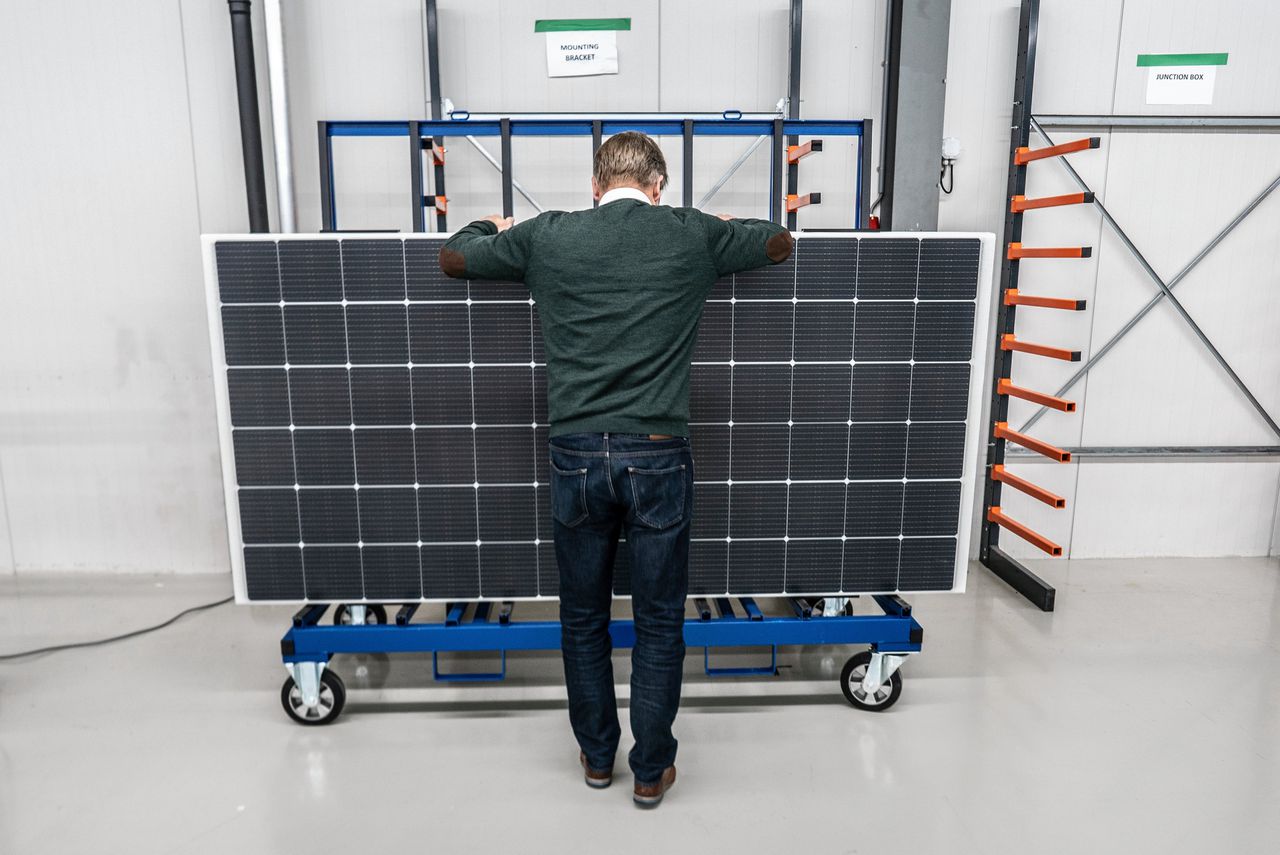
Het is een kleine twee weken voor 22 mei, de dag dat hij minister Rob Jetten (D66, Energie) en de Estse Eurocommissaris voor Energie Kadri Simson zal rondleiden. Jan Vesseur (57) loopt nog altijd met enig „ongeloof” door de fabriek in Weert: vijf hallen met nieuwe, tientallen meters lange productiemachines, op een oppervlakte van tienduizend vierkante meter. „Dit is natuurlijk waar we heel lang naar uitgekeken hebben. En als het er dan staat, is het nog wel wat imposanter dan gedacht.”
Deze maandag is de feestelijke opening van een enorme productielocatie van Solarge, een start-up die zonnepanelen maakt. De opening trekt aandacht, omdat veruit de meeste zonnepanelen uit China komen. En omdat Solarge heel andere zonnepanelen maakt dan concurrenten. Ze zijn volledig recyclebaar, de productie kost minder CO2 en ze bevatten geen PFAS. Bovendien zijn ze lichter van gewicht, waardoor ze op daken van industriële gebouwen met minder draagkracht kunnen.
Een Nederlandse zonnepanelenfabriek past in de politieke wens de productie voor de energietransitie terug naar Europa te halen. Alleen zijn de panelen wel duurder dan de Chinese. Nu de fabriek (waarin tien miljoen euro is geïnvesteerd) officieel opent, breekt een spannende tijd aan voor de start-up. Krijgt het team nog tegenslag? En zijn er genoeg klanten?
Solarge produceert en verkoopt zijn zonnepanelen al op kleine schaal in pilotprojecten, maar in de nieuwe fabriek is het de bedoeling dat er iedere negentig seconden een paneel van de band komt. Over vier weken moet dat lukken, denkt Vesseur, en aan het eind van het jaar dag en nacht, zeven dagen per week. „Dat is totaal iets anders dan nu: we maken vijf panelen op een dag.”
Effect van uv-licht op kunststof
Solarge begon in 2018 als een samenwerking tussen bouwbedrijf Heijmans, TNO, kennisinstituut Solliance en de Saoedi-Arabische kunststoffabrikant SABIC, eigenaar van Zuid-Limburgse fabrieken die vroeger van DSM waren. De technologie borduurt voort op eerder onderzoek van SABIC naar het effect van uv-licht op kunststoffen in bijvoorbeeld autobumpers. Vesseur, die eerder een bedrijf in de afvalverwerking leidde en twaalf jaar in verschillende functies bij Philips werkte, kwam in 2017 in contact met de mede-oprichters en werd de topman. Vorig jaar verhuisde het bedrijf van Eindhoven naar Weert, waar minder concurrentie is om personeel, zodat het makkelijker werknemers voor de fabriekshallen zou kunnen vinden.
In de kantoorruimte boven de fabriekshallen staat een paneel van Solarge tegen de muur, 2 meter 30 bij ruim een meter. „Probeer maar eens te tillen”, zegt Vesseur. „Gaat nog prima, toch? Deze is dertien kilo. Als dit van glas zou zijn, zit je over de dertig kilo.”
Hoe mooi het ook is dat Nederlanders hun daken massaal beleggen met zonnepanelen, over 25 tot 30 jaar zitten we met een enorme afvalberg, weet Vesseur. Dit omdat de reguliere panelen nauwelijks te recyclen zijn. „Het glas breekt snel in kleine stukjes, er zit lijm op de zonnecellen [die lichtenergie omzetten in elektriciteit]. Je kan er niks mee.”
In tegenstelling tot Aziatische concurrenten, verpakt Solarge zijn zonnecellen niet in aluminium en glas. De panelen zijn van kunststof, waardoor ze te smelten zijn, en om te vormen tot nieuwe panelen. Solarge gebruikt nu nog nieuw plastic en begint dit najaar met het gebruik van biobased plastic (kunststoffen gemaakt op basis van biologische grondstoffen). Vanaf 2024 wil het nieuwe panelen gaan maken met gerecyclede plastics.
Honingraat
Vesseur laat zien hoe het paneel is opgebouwd. „De zonnecellen zijn aan elkaar verbonden, zodat stroom over het paneel kan lopen. Normaal heb je een glasplaat aan de voorkant van de cellen, soms ook aan de achterkant. Wij vervangen het glas door kunststof. Omdat het net zo sterk moet zijn, is de plaat in een honingraatstructuur gesmolten. Een hele mooie, krachtige structuur, die weinig materiaal nodig heeft.”
De weg naar het bouwen van een grote fabriek was niet eenvoudig. Vesseur sprak afgelopen jaren meer dan tweehonderd potentiële investeerders. Makkelijk waren ze niet te overtuigen. Vooral de private equity-achtige partijen haakten af. Ze keken voornamelijk met een financiële bril, zegt Vesseur. „Van: hoe snel gaat dit zich terugverdienen?”
Het waren vooral (oud-)ondernemers die wel financieel bij het bedrijf instapten. „Die zeiden: ik geloof hierin en vind het belangrijk”, zegt Vesseur. „Natuurlijk willen ze geld verdienen, maar ze realiseren zich ook: het is een start-up. Daar zit veel meer risico aan.”
Een van de uitdagingen voor komende jaren is het vinden van technisch personeel. Nu werken er 25 mensen, maar dat moet flink worden uitgebreid. „We concurreren met ASML, Philips, DAF. Dat zijn grote spelers. En verhalen als over Lightyear helpen niet.” Lightyear is een Helmonds bedrijf dat auto’s ontwikkelt die rijden op zonne-energie. Het ging eerder dit jaar failliet en maakt nu met een flink uitgedund werknemersbestand een doorstart.
Het faillissement van Lightyear maakte indruk bij Solarge als andere groene Nederlandse start-up. Tegelijk, zegt Vesseur, zijn de bedrijven heel verschillend. „Een zonne-auto ontwikkelen… als je ziet met hoeveel geld Elon Musk elektrisch rijden populair heeft gemaakt, dat is héél moeilijk voor een nieuw bedrijf. Wij doen gewoon iets nieuws op een al gevestigde markt, die van zonnepanelen. En we hebben het jaren heel klein gehouden. We werkten hier tot vorig jaar met twaalf man in een klein kantoortje. We hebben dus veel minder cash burn [geven minder snel geld uit].”
Het draait om juiste hitte en druk
In een hal bedoeld voor onderzoek, boven de fabriek, buigen twee medewerkers zich over een paneel. De Slowaakse Lukas Simurka (35) legt zijn Roemeense collega Roxana Chirvasitu (30) uit waar ze op moet letten. Hij laat zijn vingers over de toplaag glijden om te kijken of die goed gehecht is.
Ze staan bij wat in jargon een ‘laminator’ heet, met als bijnaam de oven. „Het aan elkaar lamineren van de verschillende lagen wordt gedaan met hitte en druk”, zegt Simurka, een fysisch scheikundige.
Binnenkort verhuist hij met zijn vrouw uit Eindhoven naar Weert. Waarom koos hij voor Solarge, een bedrijf met minder bestaanszekerheid dan een gevestigd bedrijf als -ASML? „Hier had ik de kans om betrokken te zijn vanaf de vroege ontwikkeling, tot het uiteindelijke product”, zegt Simurka. „Ik kan mijn input terugzien in wat uiteindelijk wordt verkocht. Eerder werkte ik bij bedrijven met tienduizenden werknemers. Daar had ik minder impact.”
En zelfs áls het misgaat, zegt hij, „geloof ik er wel in dat ik ergens anders een baan kan vinden”.
De laminator waarbij het duo staat (minstens zo groot als een MRI-scanner) is een „heel simpel campingpitje”, aldus Vesseur, vergeleken met de machine die sinds kort in de fabriekshal een verdieping lager staat. Dat is de „drie-sterren-oven” – een soort brede buis van dertig meter lang met drie kamers. De panelen kunnen met zes tegelijk naar binnen, en er kunnen achttien panelen tegelijk doorheen gaan. Vesseur: „Dit is eigenlijk het hart van de productielijn, omdat de verschillende lagen aan elkaar gebakken worden.”
De productiemachine komt uit China, waarmee de greep van dat land op de branche van zonnepanelen ook bij Solarge nog zichtbaar is. „Het is een vergelijkbaar proces als bij reguliere zonnepanelen, alleen doen zij het met glas en wij met kunststof.”
De robot moet het precies goed doen
Momenteel wordt zo’n 80 procent van de Nederlandse zonnepanelen helemaal in China geproduceerd, blijkt uit cijfers van brancheclub HollandSolar. De zonnecellen voor de panelen haalt Solarge ook nog uit China, al wil het bedrijf die binnenkort ook in Europa gaan halen. Er staat bijvoorbeeld een fabriek in Noorwegen die ze kan maken.
In de fabriek loopt een aantal Chinezen rond, naast mensen met allerlei andere nationaliteiten. Vesseur: „Hier zie je een interessante interactie. Onze Griek, die daar met zwarte haren zo driftig aan het knikken is, staat daar met twee Nederlanders, een Spanjaard en twee Chinezen.” Ze discussiëren over de beste manier om een robot in te stellen. Het is de eerste machine op de productielijn, die de achterkant van het paneel op een loopband moet plaatsen. „We hebben van tevoren wel bedacht hoe het moet werken, maar de robot moet het natuurlijk ook precies goed doen”, zegt Vesseur.
Het precies afstellen van de machines maakt de weken voordat de fabriek overgaat op massaproductie spannend. „Alsof we de Alpe d’Huez beklimmen. We zijn er bijna, het gaat allemaal nog steeds goed. Maar komen we precies boven wanneer we willen? Of krijgen we nog ergens tegenslag?”
De eerste klanten bestaan voornamelijk uit bedrijven met gebouwen waarvoor reguliere zonnepanelen te zwaar zijn, zoals distributiehallen. Ook voor de agrarische sector geldt vaak dat ze niet te veel panelen kwijt mogen op daken van stallen.
Terugverdientijd is langer
Bedrijven die ook kunnen kiezen voor reguliere panelen, zijn lastiger te overtuigen, merkt Vesseur. De terugverdientijd is wat langer dan bij reguliere panelen. En zonnepanelen vinden mensen op zichzelf al iets ‘goeds’. „Dat werkt in je nadeel”, zegt Vesseur, „Mensen denken: het is toch al goed dat we zonnepanelen nemen? Ze maken zich ook niet druk over recycling, over wat er over vijftien jaar met dat paneel gebeurt.”
De panelen zijn volgens Vesseur, als ze eenmaal geïnstalleerd zijn, „20 à 25 procent duurder” dan panelen uit China. Solarge kan verder omlaag met de prijs, verwacht Vesseur, als de fabriek eenmaal op stoom is en ze grote aantallen kunnen produceren. Dat komt doordat een groot deel van het werk door machines wordt gedaan en veruit de meeste kosten in het materiaal zitten, en niet in de arbeidsuren.
Vroeger was dat anders in de industrie, weet Vesseur, toen zaten er veel meer kosten in het handwerk. „Ik werkte zelf voor Philips toen we een televisiefabriek vanuit West-Europa naar Oost-Europa verhuisden. We bespaarden op één televisie 25 euro aan arbeidskosten. Als je miljoenen televisies maakt, scheelt dat een hoop geld.”
Omdat arbeidskosten er minder toe doen, vindt Vesseur de politieke roep om reshoring (het terughalen van bedrijfsactiviteiten naar het eigen land) „in die zin iets heel logisch”.
Zijn bedrijf heeft de tijd mee, denkt Vesseur. „Ik heb ooit met een aantal mensen een bedrijf opgericht voor zorg op afstand via online tools. Dat deden we in 2007, en toen werden we fataal getroffen door de crisis in 2008. Dat is het grappige bij start-ups. Iedereen zegt altijd dat het team belangrijk is. Maar ik denk dat de timing nog belangrijker is. Tot twee, misschien wel anderhalf jaar geleden, moesten we iedereen uitleggen dat het niet verstandig is om afhankelijk te zijn van China voor de energietransitie. Dat hoeven we nou, gezien de geopolitieke ontwikkelingen van de laatste jaren, niet meer uit te leggen.”
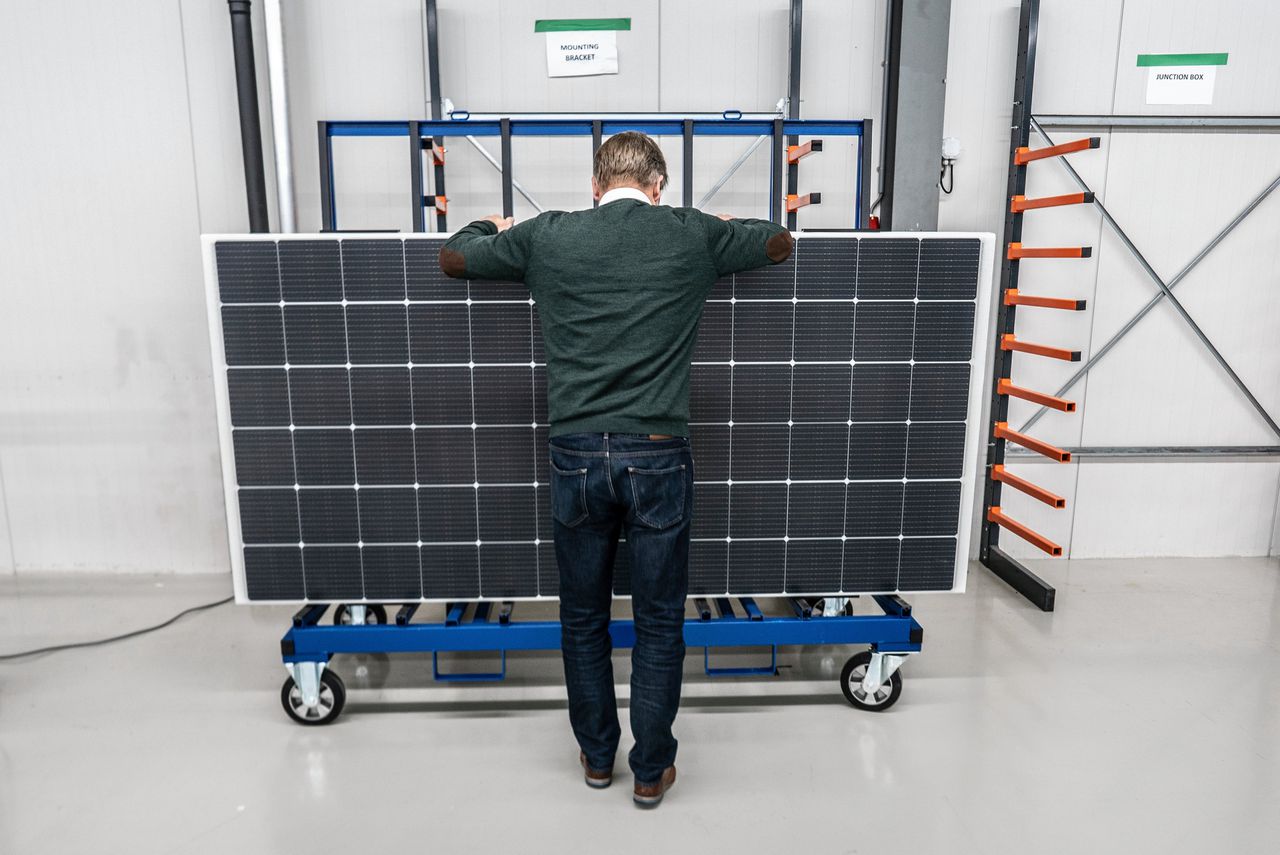