Onderweg naar de knalgele installatie waarmee start-up Paebbl binnenkort een grondstof voor hypermodern beton gaat maken, komen we langs een muur van stokoud beton vol butsen. „Het is erfgoed, beton van voor de Eerste Wereldoorlog”, zegt Ana Luisa, ‘VP of Product’ bij Paebbl en verantwoordelijk voor het product en het contact met de markt. In de muur zit een deur die ze opent met een app op haar telefoon.
Het Zweeds-Fins-Nederlandse Paebbl bestaat ruim drie jaar. Investeerders waaronder Capnamic, Holcim, Amazon en Pale Blue Dot hebben tot nu toe 33 miljoen euro geïnvesteerd. Het bedrijf – met zo’n zestig medewerkers – huist in een loods op de voormalige RDM-werf in Rotterdam. Op dit terrein barst het van de havengerelateerde innovatieve bedrijven en fieldlabs. „Met ons chemische proces passen we goed in deze omgeving”, zegt Pol Knops, mede-oprichter van Paebbl. „Hier zijn ook de juiste technici te vinden.”
Paebbl maakt een poederachtig materiaal dat iets weg heeft van cement. Maar waar cementproductie tot veel CO2-uitstoot leidt, gebeurt bij de fabricage van dit materiaal het omgekeerde: er wordt CO2 in vastgelegd.
Het poeder, magnesiumcarbonaat, is het resultaat van razendsnelle verwering van silicarijk gesteente. In de reactor van Paebbl gebeurt onder hoge druk en bij hoge temperatuur in drie uur wat in de natuur jaren in beslag neemt. Het poeder kan cement deels vervangen.
„Dit hebben we nog maar net: het is gewapend beton”, zegt Luisa glunderend, terwijl ze naar een blok beton op de grond wijst. „Dit is het echte werk, een demonstratie dat ook constructieve toepassingen mogelijk zijn met ons product.”
Luisa krijgt meer verzoeken tot samenwerking dan ze aankunnen, vertelt ze. „Dat was eerder wel anders”, zegt Knops, die al twee decennia met het idee voor Paebbl rondloopt. „Ik sprak een paar jaar geleden met dezelfde bedrijven als nu, maar toen was niemand geïnteresseerd. Nu moeten ze serieuze plannen maken om hun CO2-uitstoot omlaag te brengen en zijn wij ineens interessant.”
Zo’n 8 procent van de wereldwijde CO2-uitstoot komt van de cementindustrie. Deze uitstoot staat te boek als hard to abate, moeilijk te vermijden. Waarom eigenlijk? Er zijn wel degelijk mogelijkheden om te verduurzamen. Maar gaan die ook doorbreken?
Chemische reactie
De cementgerelateerde uitstoot is tweeledig. Allereerst is er het brandstofgebruik. De grondstof, kalksteen, moet tot 1.400 graden verhit worden en hoewel dat in theorie ook met bijvoorbeeld (groene) waterstof kan, gebeurt dit met fossiele brandstoffen. Daarnaast zit het hem in het kalksteen zelf, de chemie ervan. Dat is een fundamenteler probleem. Van het kalksteen (calciumcarbonaat) moet eerst het halffabrikaat klinker (calciumoxide) gemaakt worden. Bij die chemische reactie komt CO2 vrij; twee derde van de cementgerelateerde CO2-uitstoot.
Portlandcement, twee eeuwen geleden gepatenteerd, is tot op de dag van vandaag het meest gebruikte type cement in beton. Na toevoeging van water verandert het cementpoeder in het bindmiddel dat zand en grind – de andere grondstoffen van beton – bij elkaar houdt.
Wereldwijd wordt jaarlijks 4,5 miljard ton cement geproduceerd, waar 30 miljard ton beton mee wordt gemaakt. „De helft hiervan wordt gemaakt en gebruikt in China”, zegt Jos Brouwers, hoogleraar bouwmaterialen aan de TU Eindhoven. „In China en ook in India gaat de productie de laatste jaren enorm omhoog. De bevolking groeit en de urbanisatie is in volle gang. Een heel andere situatie dan in Europa.”
Overal grondstoffen
Beton is razend populair als bouwmateriaal omdat het in allerlei vormen te gieten is en lang meegaat zonder dat onderhoud nodig is. „Het is ook heel goedkoop”, zegt Brouwers. „De grondstoffen zijn overal beschikbaar. Kalksteen – mergel – was in Limburg te vinden en over de grens in België en Frankrijk. Ook zand en grind vind je overal.”
Hard to abate of niet, net als alle industrieën moeten ook de cement- en betonindustrie in 2050 ‘netto nul’ uitstoot veroorzaken. De Global Cement and Concrete Association heeft als doel voor 2030 gesteld dat de betonsector 25 procent minder uitstoot dan in 2020. Nederland wil koploper zijn in deze transitie. Het Betonakkoord, waarin de bouwketen samenkomt om te verduurzamen, stelt een veel ambitieuzer doel: 70 procent reductie en zo mogelijk klimaatneutraal in 2030.
Vanuit chemisch oogpunt is van alles mogelijk. Omdat de meeste CO2 vrijkomt bij de productie van klinker, is veel winst te behalen door het recept voor klinker aan te passen. Hoogovenslakken en as die overblijven na verbranding van steenkool worden onder meer in Nederland al gebruikt als substituut. Beide zijn reststromen uit de industrie, wat de beschikbaarheid relatief beperkt.
Nederland wil koploper zijn, en mikt op 70 procent reductie en zo mogelijk klimaatneutraal in 2030
Andere klinkerachtige opties die cement deels kunnen vervangen, zijn vulkanische as en gecalcineerde klei. Beide zijn ruim voorradig. Het ovenproces om er reactief poeder van te maken, vergt lagere temperaturen dan bij kalksteen.
„De milieubelasting is bij gecalcineerde klei 40 procent lager dan bij kalksteen”, zegt Brouwers. „Dat is een flinke reductie, maar je bent nog niet bij nul uitstoot. Mensen die hier streng op zijn, zijn hiermee dus niet tevreden. Een groot voordeel is dat klei in de bestaande ovens kan. Dat maakt het wel een belangrijke tussenstap.”
Helemaal zonder cement kan het ook. Dan worden bindmiddelen gebruikt die niet onder de noemer cement vallen, maar wel sterk beton opleveren: geopolymeer beton. De bindmiddelen (aluminiumsilicaten) reageren niet onder invloed van water, maar door alkalische activators zoals natriumhydroxide toe te voegen. Dan vormen zich ketens van polymeren die net als cement uiteindelijk hard worden. Een oven is niet nodig, wat een hap uitstoot scheelt.
Vulmiddel
Waar past Paebbl in dit verhaal? Het poeder dat dit bedrijf maakt is deels bindmiddel, deels vulmiddel. In het blok gewapend beton dat Luisa toont, is een kwart van het cement vervangen door materiaal van Paebbl. Luisa hoopt de bindende eigenschappen ervan te verbeteren, zodat het de helft kan worden. „Maar ook 25 procent heeft al veel positieve impact. Voor dezelfde hoeveelheid beton hoeft minder cement gemaakt te worden, en per kubieke meter beton zit er 18,7 kilo CO2 in opgeslagen.”
Luisa en Knops beseffen dat hun product soepel moet passen in het productieproces van beton om Paebbl te laten slagen. Ze hoorden van betonmakers dat het belangrijk is dat hun poeder lekker mixt, en dus sleutelden ze aan de structuur van het materiaal. En de nieuwe installatie, zojuist in gebruik genomen, werkt net als cementfabrieken met een continuproces. In tegenstelling tot de kleinere reactor ernaast, die met ladingen werkt en steeds moet opwarmen en afkoelen.
„We doen alles tegelijk”, zegt Luisa. „We onderzoeken hoe ons product zoveel mogelijk CO2 kan opnemen en we willen ons bewijzen aan de markt”, zegt Luisa. De nieuwe reactor kan 1 kiloton (een miljoen kilo) poeder per jaar produceren, genoeg voor enkele ‘echte’ toepassingen. Ter vergelijking: de grootste Chinese cementfabriek produceert op dit moment 12 kiloton per dág.
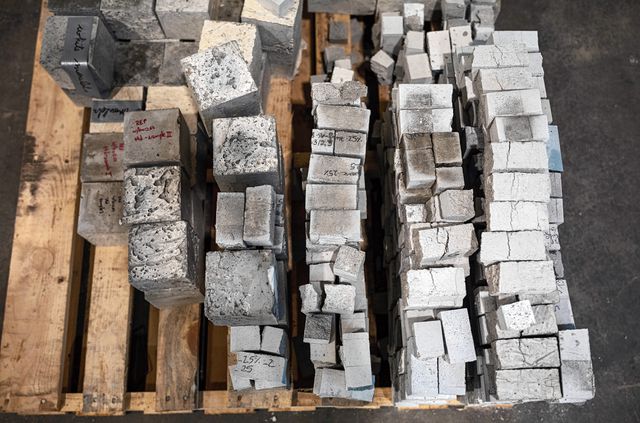
Veranderen vergt tijd
Technisch en chemisch gezien zijn er dus mogelijkheden om CO2-uitstoot te verminderen en zelfs om die helemaal te omzeilen. Waarom het dan toch moeilijk is?
„Niet alleen het product moet veranderen, maar het hele systeem eromheen, inclusief constructieve normen en aanbestedingsprocedures”, zegt Jacqueline Cramer. De voormalig minister van Volkshuisvesting, Ruimtelijke Ordening en Milieubeheer (PvdA) en emeritus hoogleraar sustainable innovation aan de Universiteit Utrecht is ruim zes jaar voorzitter van het Betonakkoord, dat in Nederland de verduurzaming van de sector voorttrekt.
Zoals in meer sectoren stelde de industrie zich in eerste instantie conservatief op, zegt Cramer. „De cementmarkt is erg gecentraliseerd. Wereldwijd zijn er zo’n acht grote cementbedrijven en die hebben veel fabrieken die ze niet zomaar willen afschrijven. Ze waren niet tegen verandering, maar zeiden dat ze zeker twintig jaar nodig zouden hebben.” Halverwege 2023 stapten de cementbedrijven uit branchevereniging Betonhuis omdat het verduurzamingstempo in het Betonakkoord werd opgeschroefd naar een in hun ogen onrealistisch tempo.
„De positie van de cementsector is anders dan die van de beton- en bouwsector”, zegt Cramer. „De verandering is heel fundamenteel, hun product is op termijn niet meer gewenst. Betonmakers kunnen overstappen naar een ander bindmiddel, de bouwsector kan daarnaast werken aan levensduurverlenging, hergebruik en circulair ontwerpen.”
Daarom geven cementmakers de voorkeur aan duurzame opties die in hun productieproces passen. „Recycling is daar ook een voorbeeld van”, zegt Cramer. „Er zijn bedrijven bezig om uit oud beton het cement los te maken. Daar zijn cementmakers enthousiast over, want dat kunnen ze eenvoudig inpassen in wat ze al doen.”
Langer in de mal
Ook betonproducenten zijn gehecht aan traditioneel Portlandcement. „Cement met hoogovenslak is minder reactief”, zegt Niki Loonen, adviseur bij bouwconcern TBI en lid van de expertgroep binnen het Betonakkoord. „Het moet langer in de mal zitten voor het hard is. In de praktijk betekent dit dat een maker van prefab-beton met Portlandcement vijf keer per week beton kan storten, en met hoogovenslak maar drie keer per week. Dan is het businessmodel naar de knoppen. Je kan tijd winnen door de mallen of de fabriekshal te verwarmen; dan hardt het beton sneller uit. Maar dit kan vaak niet zomaar.”
Wat meespeelt, is dat Portlandcement zich uitgebreid heeft bewezen. Dit is geen triviaal punt. Niemand wil een kostbaar viaduct of gebouw neerzetten dat na een tijdje niet veilig blijkt. „Onze partnerbedrijven zijn terecht voorzichtig”, zegt Cramer. „Ze hebben nu een goed product en zijn als de dood dat ze iets gaan leveren van mindere kwaliteit.”
Toch willen de betrokkenen bij het Betonakkoord van Nederland een proeftuin maken, die hopelijk ook elders verandering kan aanjagen. De strategie is dat er koplopers zijn, innovatieve bedrijven die laten zien wat mogelijk is, en een peloton – dat snel volgt als succes gebleken is.
Daarvoor moesten constructieve normen op de schop. Die zijn geformuleerd toen er alleen nog Portlandcement was. „Een deel van de normen is geschreven op basis van gebruik in de praktijk”, zegt Loonen. „Tegen roest in gewapend beton is bijvoorbeeld gebleken dat een deklaagje van 3 centimeter goed werkt. Zulke empirische data zijn er voor de nieuwe materialen nog niet. Zo komen er met nieuwe materialen allerlei variabelen bij die onbekend zijn.”
Innovatieve producten
Inmiddels is de hobbel rond normering zo ongeveer genomen, meldt Cramer in een webinar over de voortgang van het Betonakkoord. Naast bestaande prescriptieve normen, die een bepaald minimumpercentage cement voorschrijven, is er nu een parallelle standaard in ontwikkeling die is geformuleerd rond te leveren prestaties. „Voor innovatieve producten met geen of weinig cement was het anders onmogelijk eraan te voldoen”, zegt Cramer.
Nu moet de productie op gang komen. „Opdrachtgevers zijn hierbij cruciaal”, zegt Cramer. Er is wetgeving in voorbereiding die publieke opdrachtgevers in de grond-, weg- en waterbouw verplicht om steeds strengere contracteisen te stellen aan marktpartijen. Voor private opdrachtgevers gaat dit op vrijwillige basis. „Hoe strikt deze eisen in de tijd worden, hangt af van het tempo waarin koplopers hun innovaties weten op te schalen. Om hen zekerheid te bieden, hebben we met het Betonakkoord zeven grote coalities van opdrachtgevers georganiseerd die zo ambitieus mogelijk gaan uitvragen.”
Waar Cramer nog mee zit, zegt ze, is dat de koplopers nu fabrieken moeten bouwen. „Die moeten gefinancierd worden, maar ook voor banken zijn de alternatieven nieuw – en die vinden risico’s moeilijk. En betonproducenten willen zich niet vastleggen op één alternatief materiaal. We zijn er dus nog niet helemaal, maar ik ben positief gestemd.”
Uitstootloos kan nog niet
Hoogleraar Brouwers beschouwt de transitie meer vanuit internationaal perspectief, en is terughoudender: „De stand van de techniek is er nog lang niet naar dat het uitstootloos kan. De hoeveelheden cement en beton die wereldwijd jaarlijks gemaakt worden zijn zó gigantisch – alternatieven kunnen dat nog niet vervangen. Qua hoeveelheid niet, en economisch ook niet. Afstappen van fossiele brandstoffen is makkelijk gezegd, maar er is helemaal niet voldoende waterstof beschikbaar. Het is riskant normen en milieu-eisen snel zo streng te maken. Bouwen kan daardoor duurder worden. Daar hoor ik weinig mensen over. Voor starters op de woningmarkt is het nu al moeilijk, en bouwen wordt ook door andere beperkingen duurder.”
Om het uiteindelijke doel van netto nul uitstoot te bereiken zijn veel kleine stapjes nodig, denkt Brouwers. Dat is ook het beeld dat oprijst uit een vergelijkende wetenschappelijke studie naar de alternatieven voor de wereldwijde cementsector die vorig jaar is gepubliceerd. Daarin wordt het streven naar netto nul omschreven als een „ambitieuze onderneming” die om „onwrikbare toewijding van alle betrokkenen” vraagt.
„Ik denk dat deze transitie voor de cementindustrie zal verlopen langs dezelfde lijnen als het de duurzame energie vergaat”, zegt Brouwers. „In bepaalde gevallen zijn wind- en zonne-energie nu concurrerend, maar dat heeft wel dertig jaar geduurd.”
Automakers zeiden ook heel lang dat ze niet konden verduurzamen. Het kan snel gaan
De Global Concrete and Cement Association rekent daarom ook op grootschalige toepassing van technologieën om vrijkomende CO2 op te vangen en al dan niet ondergronds op te slaan (CCS). Naar verwachting zal een derde van de CO2-reductie in 2050 gerealiseerd worden dankzij CCS-technologieën. Die moeten overigens nog grotendeels van de grond komen en zijn niet goedkoop.
De CO2 kan ook hergebruikt worden. Hier komt Paebbl weer om de hoek. Omdat in zijn proces CO2 wordt vastgelegd, is het idee interessant in rekensommen om bij ‘netto nul’ te komen. De CO2 die vrijkomt in een cementfabriek, zou na afvang wellicht zelfs ter plekke in CO2-vastleggend materiaal verwerkt kunnen worden.
Dat de houding van bedrijven de laatste jaren verandert, is veelzeggend, denken Luisa en Knops. Luisa: „De wereld begon te verduurzamen bij de energiesector. Inmiddels gaat steeds meer aandacht naar materialen, in het bijzonder materialen in de gebouwde omgeving omdat die lang meegaan. Overheden stellen grenzen, maar ook gebouweigenaren vragen vaker om duurzame opties.”
Knops: „Automakers zeiden ook heel lang dat ze niet konden verduurzamen. Inmiddels moeten ze wel elektrische modellen maken, want anders houdt het voor ze op. Het kan snel gaan.”
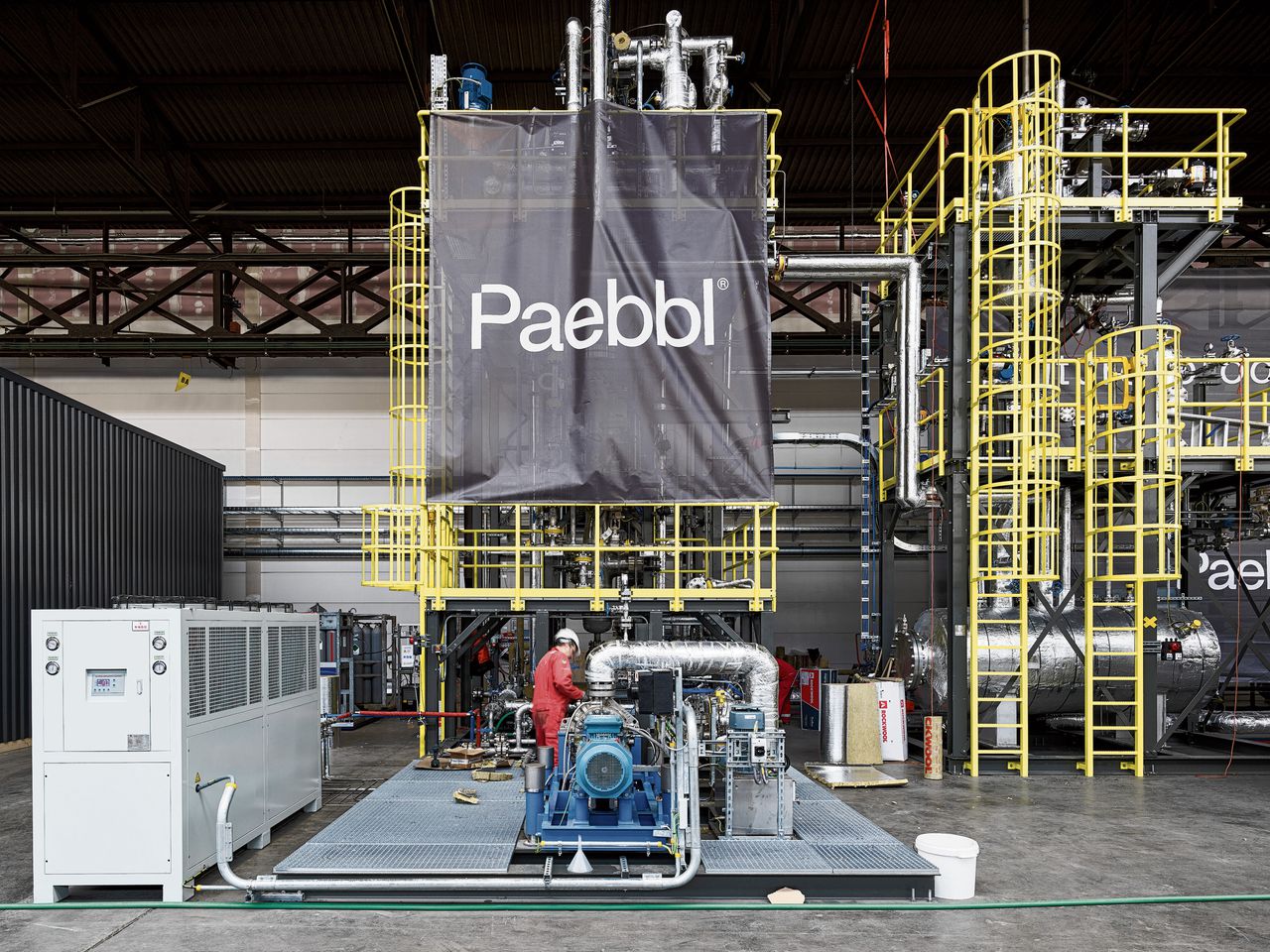