Al heeft hij een ingewikkelde baan, de carrière van Eric Beyne laat zich in twee woorden samenvatten: factor duizend. Sinds de hoofdonderzoeker in 1984 aantrad bij het Belgische imec-instituut, hielp hij de fijnmazigheid van de transistors op een chip – schakelaars die een 0 in een 1 veranderen – te verbeteren. „Veertig jaar geleden werkten we met een resolutie van 3 micron, nu is dat 3 nanometer.” Een micron is een duizendste millimeter. Een nanometer is een duizendste daarvan. Ter vergelijking: de diameter van een menselijke haar is 50 micron.
Bij het Leuvense instituut doen chipbedrijven samen precompetitief onderzoek, omdat het fabricageproces veel te duur en te complex is om het op eigen kracht te ontwikkelen. Eric Beyne is verantwoordelijk voor het 3D-programma van imec en zorgt ervoor dat fabrikanten en leveranciers van chipmachines en materialen ongeveer dezelfde bouwstenen gebruiken voor de chips van de toekomst.
De schaalverkleining is tot nu toe grotendeels te danken aan verbeteringen in de lithografiemachine, de scanner die als een kopieerapparaat ragfijne chippatronen vanaf een masker op een silicium schijf of ‘wafer’ projecteert. Het is schrijven met licht, in een moordend tempo.
De Nederlandse multinational ASML, net als imec opgericht in 1984, is marktleider in lithografie en werkt nauw samen met het Belgische instituut bij de ontwikkeling van nieuwe productietechniek. Als de scanner structuren zowel in de lengte als de breedte kan laten krimpen met 70 procent (samen 49 procent), dan passen er twee keer zoveel transistors op dezelfde oppervlakte. Dat verschijnsel is beschreven in de wet van Moore. Gordon Moore, mede-oprichter van Intel, overleed in 2023 maar werd onsterfelijk nadat hij in 1965 had opgeschreven dat het aantal transistoren op een chip elke twee jaar zou verdubbelen. Dat patroon bleef zich min of meer herhalen tot op de dag van vandaag.
Met de wet van Moore als richtlijn bouwt de industrie processors die elk jaar sneller, goedkoper of zuiniger zijn. De prijs per ‘bit’ daalt en daardoor groeit de afzetmarkt: zo belandden halfgeleiders in alle denkbare apparaten, van alarmsysteem tot afwasmachine, van koptelefoon tot koffiemachine.
Schaalverkleining zorgt ervoor dat er meer geheugen op een usb-stick past of dat chips in veel kleinere toepassingen passen. Denk aan ‘slimme pillen’ die je lichaam van binnenuit onderzoeken of chips in je hersenpan. De efficiëntie neemt ook toe: smartphones bieden veel meer rekenkracht dan tien jaar geleden, maar halen toch een dag op een volle batterij. En op een laptop met een moderne chip kun je ruim 20 uur onafgebroken werken. Dat was een paar jaar geleden ondenkbaar.
De meest geavanceerde processors tellen tientallen miljarden transistors. Fabrikant Intel denkt in 2030 zelfs duizend miljard schakelaars op één chip te kunnen proppen. De lineaire krimp – in de lengte en de breedte – gaat echter niet meer zo snel als voorheen. Daarom moet de chip de hoogte in: de derde dimensie. Als er niet meer schakelingen naast elkaar passen, dan moeten ze maar op elkaar. Maar hoe?
NRC ging langs bij experts van imec en Nederlandse bedrijven om te horen welke plannen er zijn om dat magische getal van duizend miljard transistors te halen. Nederland heeft hiervoor opvallend veel toonaangevende techniek in huis. Daarvoor hoef je maar naar de sterk gestegen beurskoersen van ASML, ASM en Besi te kijken.
Disclaimer: dit artikel beschrijft de basis en geeft maar een fractie weer van de ongelooflijke complexiteit van moderne chipproductie.
Een maandenlang proces
Digitale schakelingen zijn onzichtbaar voor het menselijk oog. Maar zoom je in, dan zie je dat een chip bestaat uit tientallen verdiepingen die elk weer uit tien laagjes bestaan: verzamelingen van transistoren met daaromheen onderlinge verbindingen en de stroomvoorziening. De doorsnede ziet eruit als een doorgezaagd flatgebouw, met liftschachten en leidingen die de verdiepingen met elkaar en met de buitenwereld verbinden. Alleen de kritieke transistorlagen worden belicht in lithografiemachines die de allerhoogste resolutie afbeelden. De overige lagen kunnen af met goedkopere lithografiesystemen, die vaak sneller zijn.
Na elke belichtingsstap ondergaat de wafer een reeks behandelingen: het wegetsen van overtollig materiaal, het toevoegen van elektrische eigenschappen met zeer kleine hoeveelheden elektrisch actieve verontreinigingen, kortweg ‘dotering’. Tussendoor wordt de schijf gereinigd, chemisch behandeld en verhit in ovens. Of moet-ie even bijkomen van al het geweld. Dan volgt weer een nieuwe laag (depositie), fotolak en belichting met een volgend patroon. Zo groeit stap voor stap een schijf vol chips, een proces dat maanden duurt. Een schijf die de fabriek verlaat heeft vaak meer dan duizend processtappen ondergaan. Dan worden de schijven in stukken gezaagd en de chips verder verwerkt. Apparaten in de chipfabriek moeten brandschoon zijn en blijven, want op nanometerniveau veroorzaakt elk stofje een fout. Naarmate de schakelaars dichter op elkaar geperst worden, verdwijnt alle speelruimte.
De fineliner van ASML
In de chipfabriek is de lithografiemachine het gereedschap dat bepaalt wat de minimale omvang van de bouwstenen is. Dat hangt om te beginnen af van de golflengte van het licht. Begin jaren tachtig werd er geprojecteerd met kwiklampen met 436 nanometer, daarna uv-licht (365 nm) en vervolgens lasers met een golflengte van 248 en 193 nanometer. Alsof je met een dunnere fineliner steeds kleinere vormen tekent.
Een andere bepalende factor is de lensopening of numerieke apertuur; hoe groter die NA, des te scherper de lijnen. Met een dun laagje water onder de lens (immersie) kun je de effectieve NA verder vergroten. De volgende stap was extreem ultraviolet licht (13,5 nm). Maar omdat die techniek van ASML jaren vertraging opliep, verkleinden chipfabrikanten de resolutie van hun structuren alvast door ze in meerdere belichtingsstappen te projecteren. De methode lijkt op een boek dat je tweemaal bedrukt; de tweede keer mik je nieuwe regels precies tussen de regels en verdubbelt zo het aantal woorden op een pagina. Deze multi-patterning-techniek is tijdrovend, vergt extra tussenstappen en levert meer defecte chips per wafer op. Maar zo kon de wet van Moore wel weer even vooruit.
In 2019 ging EUV in massaproductie en nu bouwt ASML de High NA-machine, een gevaarte van 14 bij 4 meter en ruim 4 meter hoog, met grotere spiegels en een hogere numerieke apertuur. Met die scanner kunnen fabrikanten tijd besparen omdat ze de benodigde resolutie weer in één slag maken, dat scheelt processtappen.
ASML en zijn lenzenleverancier Zeiss moesten wel compromissen sluiten voor High NA. Het beeldveld waarop het chippatroon staat is kleiner. Daardoor moeten grotere chipontwerpen in tweeën geknipt worden en daarna weer aan elkaar geknoopt: gedoe. Daarnaast projecteert de High NA-machine weliswaar scherp, maar met een kleinere focusdiepte. Dat vergt aanpassingen aan de lichtgevoelige lak; die moet een andere chemische samenstelling hebben en extra dun aangebracht worden (minder dan 20 nanometer). Ook de schijf zelf moet extra vlak liggen, om afwijkingen te voorkomen.
ASML en imec testen nu de allereerste High NA-scanner in Veldhoven. Het spannendste moment – het aansluiten en afstellen van het optische systeem – vindt rond deze tijd plaats. Daarna kunnen fabrikanten in Veldhoven ermee gaan testen. Intel staat te popelen, Samsung en TSMC gebruiken nu dubbele belichting met hun huidige EUV-machines en hebben dus minder haast om over te schakelen naar die High NA-machine, die een kleine 400 miljoen euro gaat kosten – het dubbele van een gewone EUV-scanner.
Lees ook
High-NA: zo bouwt ASML het grootste kopieerapparaat ter wereld. Wie gaat ’m kopen?
Een tuinslang en een vork
Op het kleinste niveau van de chip, de transistor, verandert er veel. De basis is de veldeffecttransistor (Engelse afkorting: FET). Die bestaat uit drie aansluitingen, de bron (source) en de afvoer (drain). Daartussen ligt een gebied dat stroom geleidt zodra je er een minieme spanning op zet via een poort of gate, een soort kraan. Zo ontstaat een schakelaar die aan of uit kan.
De transistor begon als plat vlak. Het nadeel: er lekt veel stroom weg en je moet de schakelaars ver uit elkaar houden om fouten te voorkomen. De opvolger heet FinFET: het kanaal wordt rechtop gezet, in een verticale vin. De stroom kan van drie kanten (links, rechts en boven) afgeknepen worden en dus is er minder lekkage. Maar als FinFET’s te dicht op elkaar komen treden er alsnog storingen op.
De stroom is beter te controleren als je het kanaal volledig kunt omsluiten, zoals je je vingers rondom een tuinslang legt en knijpt om het water tegen te houden. Je kunt de transistors weer dichter bij elkaar plaatsen en er gaat minder energie verloren. De grote chipfabrikanten bouwen daarom elk hun eigen tuinslang: ze gebruiken daarvoor namen als gate-all-around (GAA), RibbonFET of nanosheets. Om een grotere stroom te verkrijgen worden er meerdere tuinslangen boven elkaar geplaatst. Zo krijgt de transistor een 3D-vorm.
Imec ontwikkelt de forksheet, om de transistoren nog dichter tegen elkaar te plaatsen, met een isolerend muurtje ertussen. Deze vorkvormige constructie slaat de brug naar een volgende hoogstand: het stapelen van transistoren. Die technologie, CFET of Complimentary FET genaamd, doet rond 2032 zijn intrede. Dat vergt wel een grondige verbouwing; de onderste transistor krijgt spanning van de achterkant van de chip, door de wafer heen. Daarvoor wordt de wafer in een later stadium weggeslepen tot een flinterdunne laag. CFET stapelt N- en P-transistoren – de ene werkt met negatief geladen elektronen, de andere met een positieve lading, de zogeheten ‘gaten’. Om kleine elementen als nano-sheets te bouwen, gebruiken Samsung en TSMC zogeheten 2- en 3-nanometer-procedés. Intel rekent zelfs in ångström, een tiende van een nanometer. In werkelijkheid is de pitch, de afstand tussen de transistoren, vijf tot tien keer groter dan de marketingnamen die fabrikanten bedenken. De kleinste afstand die ASML kan projecteren met ‘gewoon’ EUV is 13 nm, met High-NA is het 8 nm.
Atoom per atoom
Naast horizontale schaalverkleining moet ook de derde dimensie op de chip krimpen om nieuwe transistortypes te vervaardigen. Het is een kwestie van nog nauwkeuriger laagjes leggen en overtollige elementen verwijderen, ook op de moeilijk bereikbare plekken. Sommige onderdelen van de 3D-transistors steken uit en moeten aan de zijkant of onderzijde bewerkt worden. De oplossing komt van het Nederlandse ASM, opgericht in 1968, en inmiddels marktleider in atomic layer deposition (ALD). Dat is de vakterm voor het aanbrengen van nieuwe lagen op een chip, atoom voor atoom.
Lees ook
Topman ASM: Nederland heeft de sleutel tot de chipindustrie
De ALD-machine is een reactor waarin in hoog tempo gaspulsen worden losgelaten. Deze gassen reageren met de oppervlakte van de wafer en creëren een dunne film van één atoomlaag dik. Depositiemateriaal dat niet gebruikt wordt, wordt snel uit de reactor geblazen om plaats te maken voor de volgende puls. En dat vele keren per minuut, als een mitrailleur die atomen afschiet. Zo groeit er in minuten een uniforme laag van enkele nanometers, in alle hoeken en gaten van de chip. Precies de nauwkeurigheid die nodig is voor de chips van de toekomst.
De nieuwe transistors vergen ook veel hulplaagjes die met tijdelijke steunbalken de stapel overeind moeten houden. Vergelijk het met een 3D-printer; die kan ook niet zomaar in de lucht printen. Delen van de geplaatste lagen moeten zorgvuldig weggeëtst worden en dat kost extra stappen. Onder andere Applied Materials, een Amerikaanse fabrikant van chipmachines, en Tokyo Electron leveren de etsmachines die met gas en chemicaliën de chip te lijf gaan.
Terwijl de lithografiemachine stapsgewijs telkens een deel van de schijf belicht, behandelen de depositie- en etsmachines de volledige schijf in één keer. Tussendoor moeten de wafers wel elke keer gemeten worden, om te kijken of de behandelingen geen elektronische fouten opleveren. De gangbare metrologie gebruikt optische sensoren en elektronenstralen, die steekproefsgewijs defecten zoeken. Ook ASML produceert zulke meetapparatuur, zoals een multibeam-machine die nu met tientallen elektronenstralen tegelijk meet, straks zelfs met duizenden tegelijk.
Dat levert een grote datastroom op om het fabricageproces te kunnen optimaliseren. Elke chipfabriek verandert daardoor zelf ook in een datacenter, vol snelle chips. Het Rotterdamse bedrijf Nearfield Instruments voegt nog een slimme akoestische meettechniek toe. Gevoelige antennes ‘luisteren’ naar geluidsgolven die de lagen van een wafer kunnen penetreren, als een naald die een langspeelplaat aftast. Zo kun je ‘ondergronds’ op zoek naar elektronische fouten die je anders zou missen.
Plakken en stapelen
Om meer transistoren in één verpakking te combineren ontkomt de chipindustrie niet aan het combineren van gespecialiseerde chips. Zo’n schakeling is niet langer ‘monolitisch’, gebouwd op één onderliggende laag of ‘substraat’, maar bestaat uit een verzameling van apart geproduceerde onderdelen.
Dat principe is niet nieuw. Eric Beyne van imec herinnert zich de vroege jaren negentig, toen fabrikanten zogeheten multichip-modules gingen maken. „Toen brachten we apart geproduceerde chips samen op een ander soort substraat. Maar het tempo van de lineaire schaalverkleining lag zo hoog dat het niet langer nodig was multichips te maken.”
Voortgedreven door die schaalverkleining combineerden chipontwerpers functies uit de hele computer (processor, snel geheugen, grafische chip) in één zogeheten system-on-chip of SOC’s. Die vind je bijvoorbeeld in smartphones. Omdat de schaalverkleining tegen zijn grenzen aanloopt bij sommige toepassingen, zoals SRAM-geheugen, veranderen de ontwerpen: het is handiger om verschillende chips weer los van elkaar te produceren en ze later samen te voegen in één gecombineerde verpakking.
Met name generatieve AI, zoals OpenAI die gebruikt voor ChatGPT, vreet rekenkracht en opslagcapaciteit om data te trainen. AI-chips, bijvoorbeeld van Nvidia of AMD, zijn grafische processors met daarnaast een stapeltje breedbandgeheugen. Dat is geheugen gemaakt van DRAM-chips die op elkaar gelegd zijn en snel communiceren met een aansturingsmodule eronder. De duurste Nvidia-processor van dit moment, de H100, kost ongeveer 40.000 dollar.
Lees ook
van videokaart tot supercomputer; de AI-revolutie geeft Nvidia vleugels
De H100’s worden ook aan elkaar geknoopt in één systeem tot een draagbare supercomputer, die het tienvoudige kost en ruim dertig kilo weegt. Apple doet het op kleinere schaal met zijn Ultra-chips, en koppelt twee verschillende chips tot één megaprocessor met meer dan 100 miljard transistors.
Door functies op te splitsen in chiplets, zoals deze losse modules heten, kun je geheugen, processors of signaalverwerking elk met zijn eigen optimale productietechniek maken. Dat levert minder foutieve chips op, en dus minder verlies per wafer. Je kunt bovendien even doorgroeien, door meer chiplets te koppelen op één plak, met een verbindende brug eronder.
Chiplets zijn verbonden via interconnects die meestal volgens de UCIe-standaard werken. „Zie het maar als een usb-stekker die uiteenlopende apparaten verbindt”, zegt Eric Beyne. Voor de chipontwerpers, zegt hij, lijkt het alsof al die verschillende onderdelen toch nog op één fysieke chip staan. Er is wel een nadeel; als de onderdelen van chips fysiek verder van elkaar verwijderd zijn, duurt het langer om signalen te transporteren van de ene naar de andere kant. Dat kost dus rekentijd. Straks zou je volgens Beyne de chiplets ook kunnen koppelen met fotonische chips. Dat opent de deur naar snellere dataverbindingen en dus minder vertraging in de gegevensoverdracht.
Sommige geheugentoepassingen zijn al gestapeld, zoals NAND, de chips die je voor dataopslag op usb-sticks of harde schijven gebruikt. Hun herhaalde structuur wordt zo hoog dat het flatgebouw van honderden verdiepingen begint te wankelen. Dan kun je beter twee van die losse chips op elkaar plakken. Ook de camerasensor in je telefoon is zo op elkaar geplakt, met aan de ene kant een beeldsensor en de andere kant de processor.
De chiplets vergen wel extra nabewerking in de fabriek. Eerst wordt de wafer flinterdun afgeslepen – een specialiteit van het Japanse bedrijf Disco – en vervolgens zorgvuldig op elkaar gelegd en verbonden via koperen kanalen, met een nauwkeurigheid van enkele honderden nanometers. Het Nederlandse bedrijf Besi maakt de hybride verlijmingsmachines die daarvoor nodig zijn. Besi ziet zijn omzet snel groeien omdat de hele industrie zich op ‘advanced packaging’ stort, de verzamelterm voor het combineren van losse chips in één verpakking. Zoals Eric Beyne het omschrijft: „Ooit was packaging het achterkamertje van de chipindustrie, nu zie je dat grote fabrikanten het meest investeren in deze technologie. Het achterkamertje wordt de ultraschone cleanroom ingezogen, naar de kern van de geavanceerde chipproductie.” Dat is de enige manier om, samen met de andere innovaties, over zes jaar die magische grens van duizend miljard transistors in één chip te kunnen doorbreken.
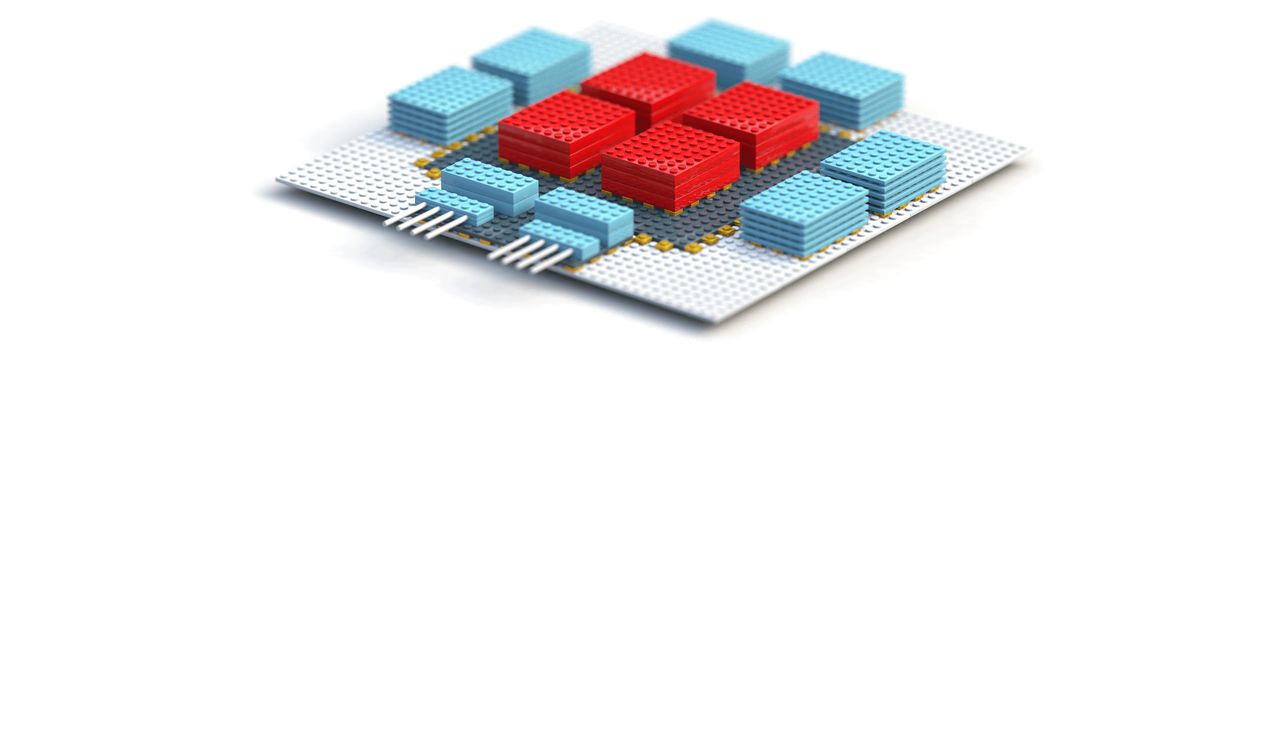